Medical Device Packaging Validation | Compliance Group Inc
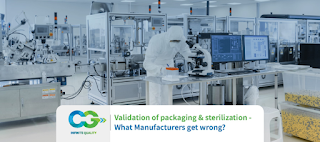
Medical Device Packaging Validation is a crucial process in the development and manufacturing of medical devices. Packaging validation ensures that the packaging system for a medical device is designed and tested to meet the necessary requirements, including regulatory standards, to ensure the safety and efficacy of the device. The packaging of a medical device plays a critical role in maintaining the integrity of the product throughout its shelf life and during transportation. Here are key steps and considerations in the validation of medical device packaging: 1. Regulatory Compliance: - Understand and comply with relevant regulatory requirements, such as those set by the U.S. Food and Drug Administration (FDA) or the European Medicines Agency (EMA). 2. Packaging Design: - Develop a packaging design that considers the specific needs of the medical device, such as protection from environmental factors, sterility requirements, and any unique characteristics of the device. 3. Mate